In an era of cutthroat competition in the electronics manufacturing industry, it is extremely important to utilize the different rapid-prototyping techniques to the fullest in order to make sure the journey of prototype to production is seamless and faster delivery is assured.

To deliver every electronic product design iteration, in time, the printed circuit board [PCB] is the most important and crucial base. The design of a PCB is a complex piece in the system since its design is driven by:
The selection of components
Layer stack specification
Impedance matching applied
Length matching applied
Overall power to which the PCB is subjected
Compliances required and
Edge cut of the board which is defined by the enclosure design and HMI elements
Due to these parameters, the design of PCBs often becomes the last task to be ticked off in the project plan and utilizes the maximum time in the project timeline.
The situation further worsens when you need the system to clear EMI/EMC tests, which are almost mandatory in every medical device and other critical applications. This leads to a situation where we need to modify the PCB design at the eleventh hour and have quick testing requirements.
This is where modern rapid PCB prototyping techniques come into the picture.
Today in 2023, we are witnessing electronic hardware development and manufacturing at an extremely rapid pace. One of the many factors which are contributing to this is the access to these PCB rapid prototyping techniques.
Being a start-up, working on complex systems with a focus on medical devices, projects often have high-density integrated circuits, sensors driven by micro currents and voltages, battery-powered systems, wireless capabilities, etc. it is important we utilize the prototyping using appropriate processes. These processes ensure that we can have a fast turn-around, minimum risk in the design error generation, and a stable design with DFM readiness. Following certain industry-accepted processes, ensure we can avoid some of the known setbacks.
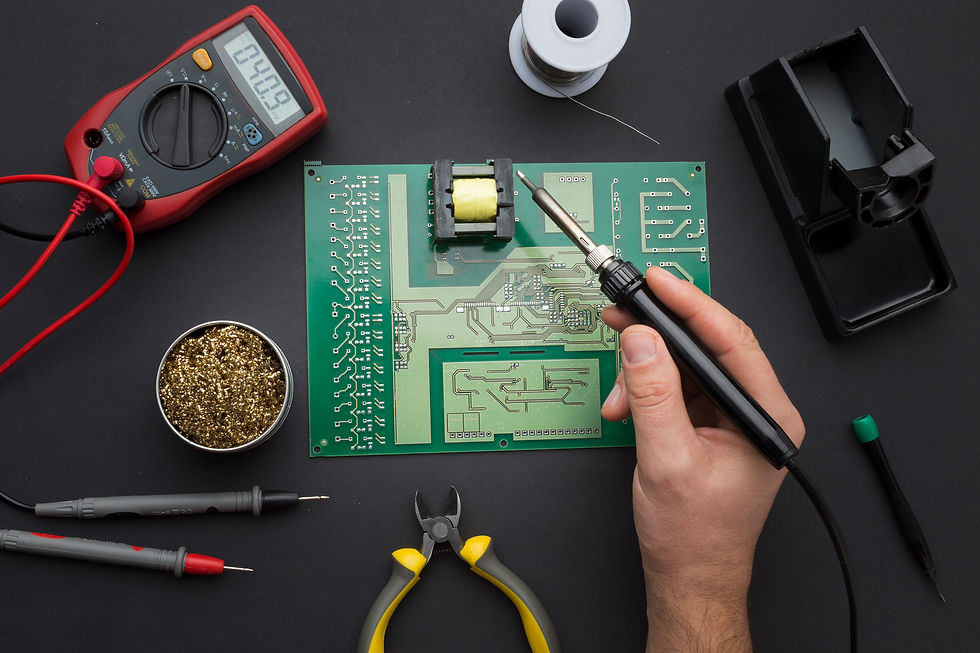
Reduced layer design
During the initial stages of prototyping, it is preferred to have fewer layers, preferably 2-4 layers. This could also be at the cost of a slightly larger PCB size. This eliminates debugging problems in the buried layers, which can be extremely difficult and might require complex optical inspection machines. This might not be possible in all the designs, however, if it can be achieved then it is possible to identify the problems at an early stage.
Sub-layer access
In events where we need sub-layers mandatorily, it is important that test points are brought out from the sub-layer to the top or bottom layer. This ensures the plane voltage or signal integrity can be checked. Failing to do so, might render the board useless, and ‘jugaad’ tricks might need to be employed which often involves breaking tracks and planes.
Overpopulated test points
In early design phases, it can also be recommended to have multiple test points. These test points might vary from design to design. But it is better to have test points for all the necessary sections such as power supply, communications including I2C, SPI, etc., along with these it is important to have test points for the different sub-systems as well.
Breakpoints on a critical or untested system
Often for research projects or non-standard projects, it will be possible we are introducing a completely new part or IC. There should be an option to eliminate this from the design completely. We do this by employing extended tracks which are broken mechanical or by having jumpers.
Adhering PCB layout to datasheet recommendations
Datasheets in most cases for electronic components provide a component placement and footprint with dimensions etc. There is a natural preference to use the footprint which is easily available in our ECAD software which makes the design process faster. However, every component is different, and we should not miss this detail.
Reusing system block from existing owned design
Most electronic systems have blocks with the same functionality, such as power supply, communication, or display elements. It is better to use tried and tested blocks wherever recurring. Also, the components for these designs will be available easily. However, this might vary with the core rating that is required.
Having a modular system design approach across different project
Despite the best practices employed, there is a decent possibility a sub-block failed in the design. In this situation, having a modular design saves the day. The whole idea of having a modular design is to have a system architecture that follows the same power supply protocol, or the connection is easy to swap, and communications have the same logic level. This allows you to change the system block overnight, without disrupting the complete system.
Identifying reliable PCB Designers
And the most important in every PCB design is identifying the right manufacturer. PCB manufacturing is mostly outsourced, given the huge capex in getting these machines and having them running. When it comes to selecting the right PCB manufacturer, it is important to consider the following parameters:
a. Quotation process – Preferred to have an online quote process
b. Flexible lead times – Having multiple lead times option, as early as 24 hours
c. Faster shipping – Reputed freight delivery available
d. AOI and QC process – A QC report must be delivered with every delivery
e. Production options – Desirable the vendor can support production volumes as well
f. Certifications – Prefer ISO, RoHS, UL compliant manufacturers
As most designers would say, ‘PCB Designing is an art, which is mastered with every failed design’, we have failed a lot to ensure that your R&D projects don’t have to.
If you want to have a dialogue to know more about our design and development journey, feel free to reach out to us at info@lifeboundtech.com
Comments